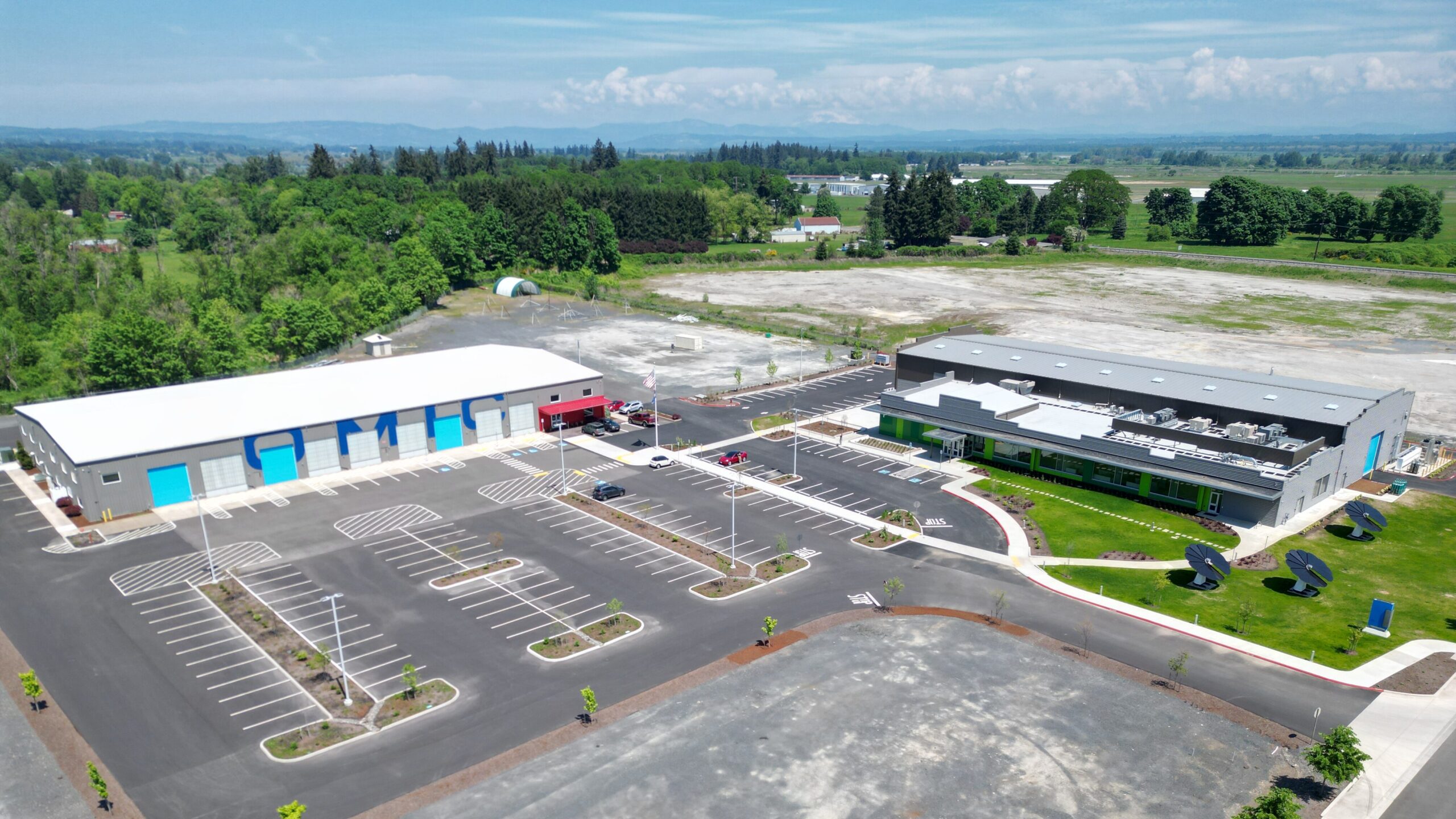
In 2017, the Oregon Manufacturing Innovation Center Research and Development (OMIC R&D) embarked on a journey that would redefine its research and development processes surrounding machining and CNC work. At its inception, OMIC R&D bore little resemblance to the powerhouse of innovation it is today. The team was smaller, and many of the key members who have since had a part in driving the institution to new heights had not yet joined. This is the story of how a nascent idea, challenged by initial setbacks, laid the groundwork for a revolutionary approach to research and development in manufacturing.
The catalyst for OMIC R&D’s transformative journey was a challenge posed by its industrial partners: to eliminate reaming in holes less than or equal to 1/2 inch in diameter in aircraft materials, specifically 4340M steel, Ti6Al4V titanium alloy, and 7050 aluminum blocks. It’s a challenging problem faced by many industrial players – hole making is a necessary process for any manufacturing process. Traditionally, any hole made that requires a tolerance of +0.0 / -.001” require the use of a drill, followed by a reamer to clean up the process.
In 2017, a claim that state-of-the-art carbide drills could eliminate the need for reaming, achieving holes with tolerances as tight as +0.0 / -0.0006”, captured the attention of the industry. This assertion, if proven true, could revolutionize precision machining and offer a significant leap forward in manufacturing efficiency and quality. However, in the world of industrial manufacturing, where the stakes involve not just advancements in technology but also substantial financial investments and operational overhauls, claims demand rigorous validation.
Members of the OMIC R&D board knew that evidence is its keystone. The pursuit of innovation, especially one that could set a new standard in manufacturing, necessitates a foundation built on solid, empirical evidence. This meant not only verifying the capabilities of these carbide drills but also understanding the implications of their widespread adoption in industrial settings. The leadership of OMIC R&D also recognized this as a potential project that could put OMIC R&D on the map. This was potentially industry changing research, especially in the world of and they wanted to take an active role in determining its validity.
This challenge was brought to Urmaze Naterwalla who served on the tech board at the time as a representative of Boeing. Matt Carter and Bill Gerry, both of whom were members of the governing board at OMIC R&D at its inception, wanted to get Urmaze and his machining expertise on this project from the get-go. After deliberating and coming to recognize the potential impact of solving this problem, they presented it to the OMIC R&D tech board, sparking interest from six cutting tool manufacturers: Kennametal, Mitsubishi Materials, OSG, Sandvik Coromant, SECO, and Walter were all invited to be an active participant in the project.
Despite the initial enthusiasm, the project soon encountered significant obstacles. The absence of effective leadership on the project led to a paralysis that ultimately halted the project’s progress. It was a period of uncertainty, where the vision for a collaborative R&D process that bridged academia and industry seemed distant. Urmaze recalls “Industry and academia were not acclimatized to working in the field of machining. It was difficult to bring key decision makers to the table for this kind of work.” As a result, the project was put on the back burner for an extended period of time.
However, the tide turned with the arrival of new leadership. Galvanized with a desire to get this project off the ground, Urmaze approached Professors Chien Wern, Burak Sencer, and Yubin Lee of Portland State University and asked them to engage in the project. Their involvement brought a new perspective and the necessary drive to revive the project, and underscored the critical role of academia not just in leading such projects but in fostering a collaborative environment where industry partners could contribute meaningfully to the research process.
To maintain impartiality and ensure the integrity of the findings, the identities of the six industrial partners tools utilized in the project were kept confidential. This anonymity allowed OMIC R&D to act as an unbiased intermediary, analyzing the results to better benefit the entire manufacturing industry. This principle of impartiality is at the core of OMIC R&D’s philosophy and utilized to this day for all projects undertaken on its floor. Urmaze, now the head of research, has been a vocal advocate for this approach, emphasizing that the moment OMIC R&D engages in IP it would lose its essence.
“As soon as we start implementing IP, I am walking out the door,” He laughs, before clarifying “While it sounds like a joke, I am quite serious. The work we do is imperative to the advancement of industry. If we start hiding our findings, what is the point of our work?”
The Precision Hole Making project took shape and expanded significantly, both in scope and ambition. To ensure the findings were accurate, participating manufacturers supplied three drill sizes, .125”, .25”, and .5”. Each tool made 100 holes in a process repeated three times for the steel, titanium alloy, and aluminum blocks to gather extensive data. The researchers in turn were able to collect data on the hole diameter tolerances, surface finishes, chip breaking, and tool wear over the course of the hole making. This meticulous approach ensured that the results would be comprehensive and applicable across the industry, and it became a testament to the power of big data in manufacturing research at OMIC R&D.
Since this was still the very beginning of OMIC R&D, this also allowed OMIC R&D to establish operating parameters and yield repeatable reliable performances on its machines. It was a process that is still repeated to this day on all projects being implemented on the floor.
The results were remarkable. As the hole sizes increased, regardless of the material being drilled, the overall quality of the hole tended to decrease. Tool wear and damage was also found in some quarter inch and half inch diameter drills. But the result did showcase that with the use of modern-day high-performance drills, the reaming operation could largely be eliminated from the process altogether. This was not necessarily the case with all tools provided by the participating cutting tool suppliers, but it was possible.
“But that is important too,” Urmaze clarified. “This isn’t about saying one tool is better than others, which was certainly a result of the project. This was about explaining why some tools were better than others, and giving all the participants data as to why that is the case.”
The culmination of this project was a moment of pride for OMIC R&D. Urmaze’s presentation of the tangible results to each participating entity marked the beginning of a new era of collaboration. While each of these participating members were direct competitors, there was an established atmosphere of collaboration during the project. The findings of this research showcased that a rising tide floated all boats. Just because some cutting tool manufacturers were not able to produce the results it promised, it could take the results back to its leadership team to adjust its tool components so it could achieve those results in the future.
“That was the proudest moment of my career at the time,” Urmaze said. “It was not about delivering good or bad news – it was about providing evidence that could help all six of these members create better cutting tools. We saw it happen firsthand, and it was exciting to see that change happen right in front of us.” It was an affirmation of OMIC R&D’s capacity to not only navigate the complexities of R&D but also to foster a culture of open innovation and shared success.
This project, sometimes referred to as “the first rabbit to run through the mechanism,” was more than just a successful research initiative. It was a defining moment that shaped the methodologies and processes OMIC R&D employs today. It set a precedent for how challenges should be approached, solved, and shared, ensuring that no stone is left unturned in the pursuit of innovation.
OMIC R&D’s journey from its initial rocky start to becoming a beacon of collaboration in machining and CNC work is a testament to the power of persistence, leadership, and the collaborative spirit. It stands as an inspiration for academics, researchers, and entrepreneurs aiming to make their mark in the R&D field, proving that with the right approach, even the most daunting challenges can lead to groundbreaking success.