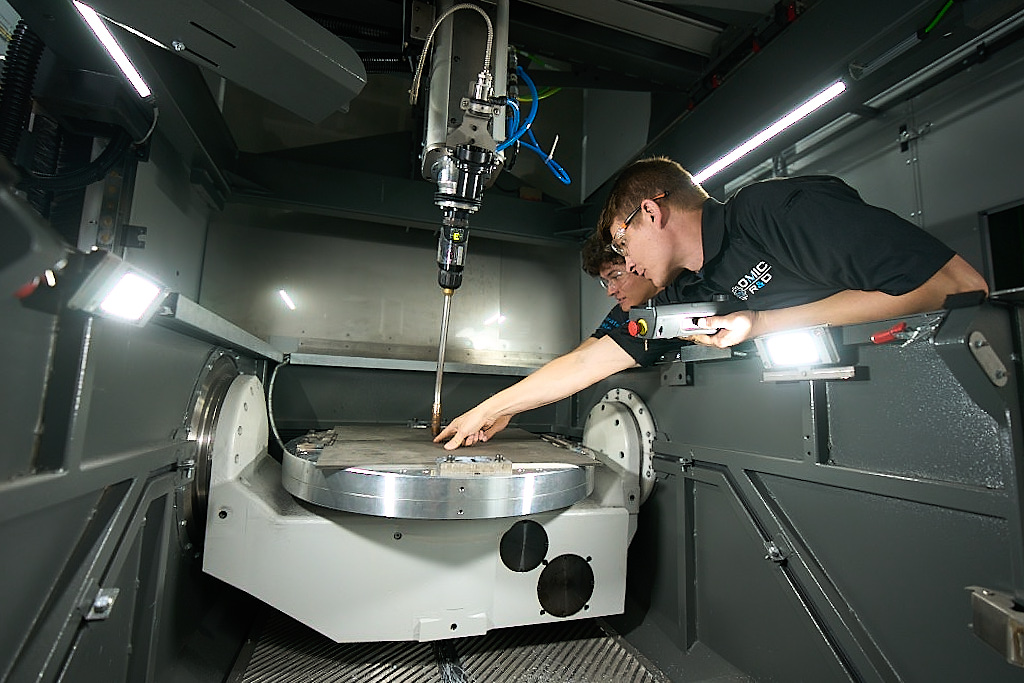
The manufacturing catch phrase ‘Near-Net-Shape’ has been a driving force in machining (subtractive) manufacturing since the early 1980s. It is the simple concept that the closer a forging is in size to the finished part that will be machined from it, the shorter machining time and less material waste that results.
In the aerospace industry the ratio difference between the starting material and the finished part is referred to as the buy-to-fly ratio. For some manufacturers that ratio can exceed 10 to 1, investing over 80% of the machining time in excessive material removal/roughing operations.
The goal for forgings, however, have been to provide enough quality material in the forging (casting) to produce the part, forging yards or casting foundries have not been provided with a good business case to reducing the buy-to-fly ratios.
In recent years, there has been a palpitating tension; an unspoken excitement amongst machinists, as the additive manufacturing industry makes its turn towards true Near-Net-Shape parts. Additive manufacturing is emerging as a viable production scale manufacturing method for production ready parts.
This is a significant leap from its humble origins in plastic prototyping scaled models, visual aids, and toy parts. Combined with more advanced additive processes like welding, wire arc additive manufacturing (WAAM), binder jetting technology, carbon fiber reinforced polymers (CFRP), friction stir welding, and robotics; additive manufacturing is making its mark as the mode of future operations.
Creating additive parts with industry relevant metals such as steel, aluminum, titanium, and stainless steel (and many others) is now a mainstream deliverable by the additive industry. Combining these additively manufactured parts with the appropriate post-processing treatments can yield material strength and integrity on par with any traditional raw material manufacturing technology.
Additive manufacturing still has challenges to overcome though.
Delivering high volume of parts at the pace of forgings, meeting finish tolerances, and surface finish, and automating post-production processes all continue to be opportunities for improvement. Nevertheless, the last decade has seen tremendous improvements in this arena of manufacturing, and more are on the horizon. The big observation is that additive manufacturing can create metal parts, with material integrity, and deliver true Near-Net-Shape often with buy-to-fly ratios of 3:1 and even 2:1.
But this in no way suggests that machining applications are on the way out.
Additive and subtractive manufacturing processes need not be looked upon in separate competitive silos. In fact, machining will be a vital, complementary part of the future state of additive manufacturing. Machining is on the verge of a significant technological revolution to accommodate the demand for this change.
As additively manufactured Near-Net-Shape parts become a viable starting point for machining operations, the need for heavy roughing will take a back seat to advancements in semi-finishing and finishing operations.
Imagine a future state where roughing operations are obsolete. Machine builders will be challenged to deliver machine tools with significantly faster spindle speeds and axis drives for heightened feed rates, without sacrificing accuracy.
This, in turn, drives the need for enhanced controller capability. The combination of lightened cutter engagement conditions and heightened speeds will place a higher emphasis on spindle power rather than torque. Cutting tool manufacturers will need cutting materials able to survive machining at heightened speeds and feeds.
Ultimately these changes must be coupled with the best practices in machining (such as proper presetting, coolant delivery, balancing, etc.), calling for an increased focus on advanced training. These challenges are by no means easy.